
Research and Development
Rich experience, unique design concept, advanced testing technology, and years of technology accumulation and cooperation and absorption of foreign advanced technology have enabled our technology to maintain the international leading level and lead the industry.

Testing Equipment
The details determine the success or failure, professional manufacturing, and many years of ready-made experience, making the German BOSCH (Bosch) Group and Swiss Swiss Watch Group trust the company's reliability and stability of HUMO products. Each product has dozens of processes, each process is constantly improving.

Quality Management
In the production process, we have always emphasized the details, details, years of field experience, accumulated valuable experience, continuous innovation, continuous improvement, continuous testing, and achieved the high-end and high-quality positioning of HUMO brand today.
Company Profile
Zhejiang HUMO Polishing Grinder Manufacture Co.,Ltd. was established in seventy's of 20th century. Currently HUMO has 7 production sites which cover the total area of 216,000 square meters, and puts out over 70,000 metric tons of mass finishing media products (ceramic media and plastic media), 6,000 units of finishing machines and 30,000 tons of polishing compounds annually. Our products sell well at home and abroad, such as USA, Japan, Korea, Germany, Switzerland etc, over 50 countries.
It has become the largest manufacturer and export base factory for mass finishing products in the world.
Based on more than 30 years of experience in the industry, the company has also actively penetrated into related industries in the field of technology in recent years – wear-resistant ceramic zirconia beads and dispersants for ultra-fine grinding. This product is mainly suitable for ultra-fine grinding of non-metallic mineral powders such as heavy calcium carbonate, kaolin and talc. The company selects high whiteness and high-fineness raw materials to ensure non-contaminated materials, and adopts a unique roll-forming process to improve the sphericity and density of the products, ensuring no cracking, combined with advanced kiln firing technology. The long-term high-temperature sintering forms a wear-resistant microcrystalline structure, which ensures stable performance during use. Among them, zirconia microbeads have high specific gravity, high efficiency, high toughness, good impact resistance, good chemical stability, and low wear on mechanical equipment.
The specific gravity can reach 4.0g/cm3 or even 6.0g/cm3, Rockwell hardness. Up to 118-124, the wear is no more than 0.0028% per hour. It is applied to high-end fields of fine processing related to minerals, chemicals, paints, machinery and electronics, filling domestic gaps, replacing imported products and exporting foreign exchange. After the launch of related products, it has been well received by the market. After several years of hard work, it has already occupied 80% of the national market share of the industry.
Products
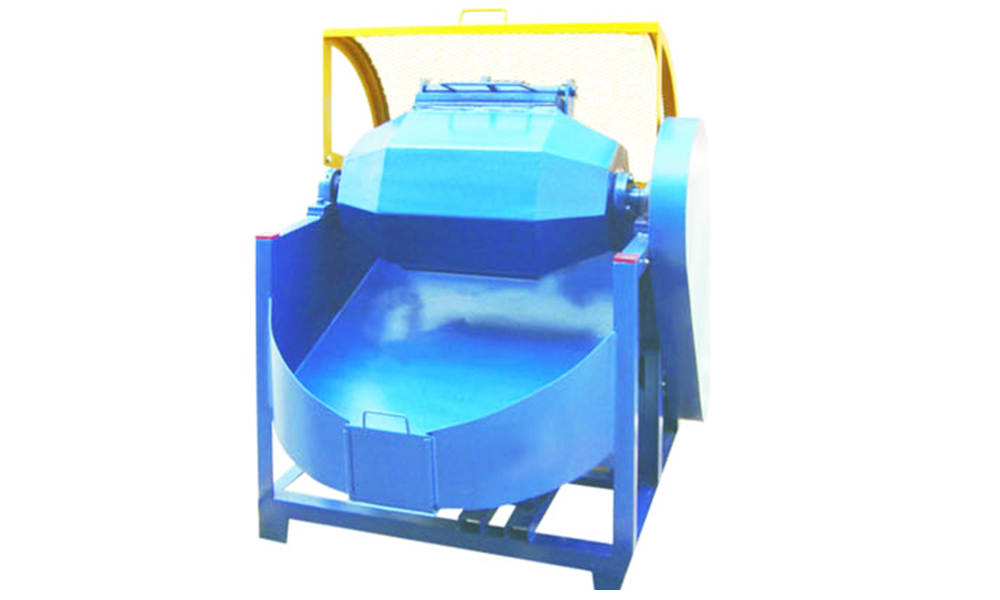
1.Posses of frequency converter,time controller,ensuring operation process steady and uniform finishing quality.
...
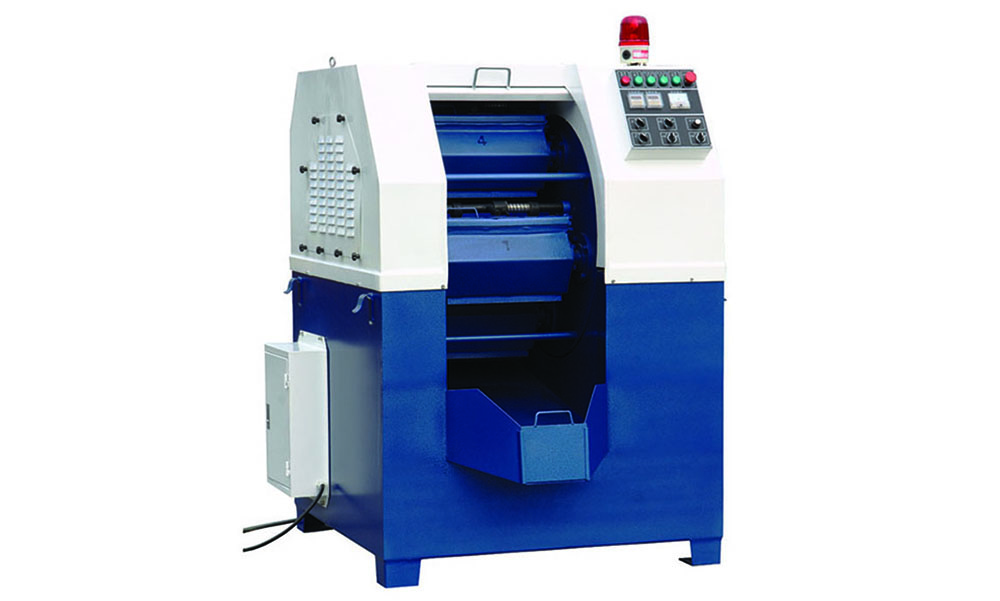
1.High wear resistant thermal-set PU lining barrel
2.Optional 8°high efficiency tilt bar...
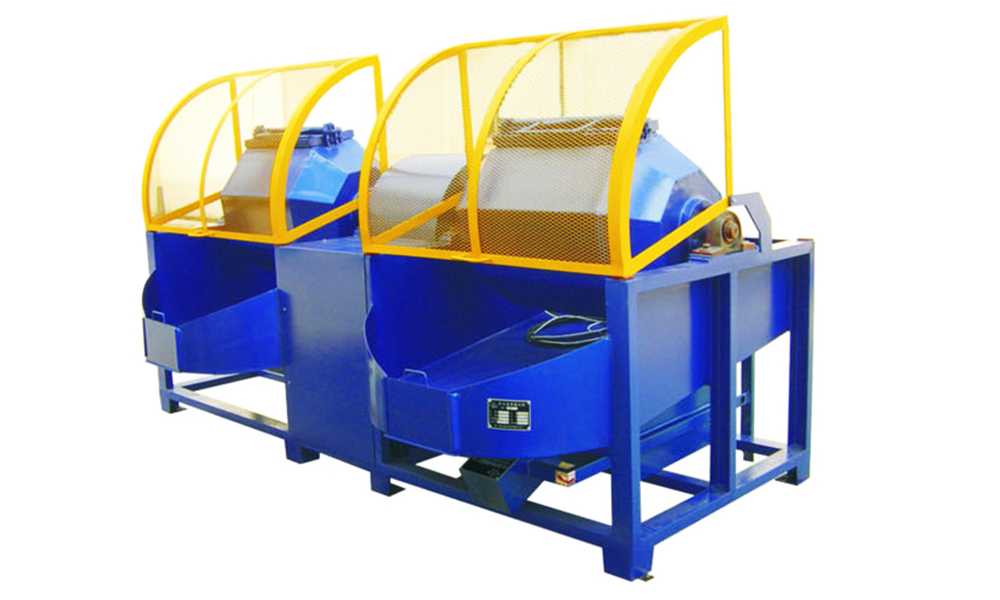
1.Posses of frequency converter,time controller,ensuring operation process steady and uniform finishing quality.
...
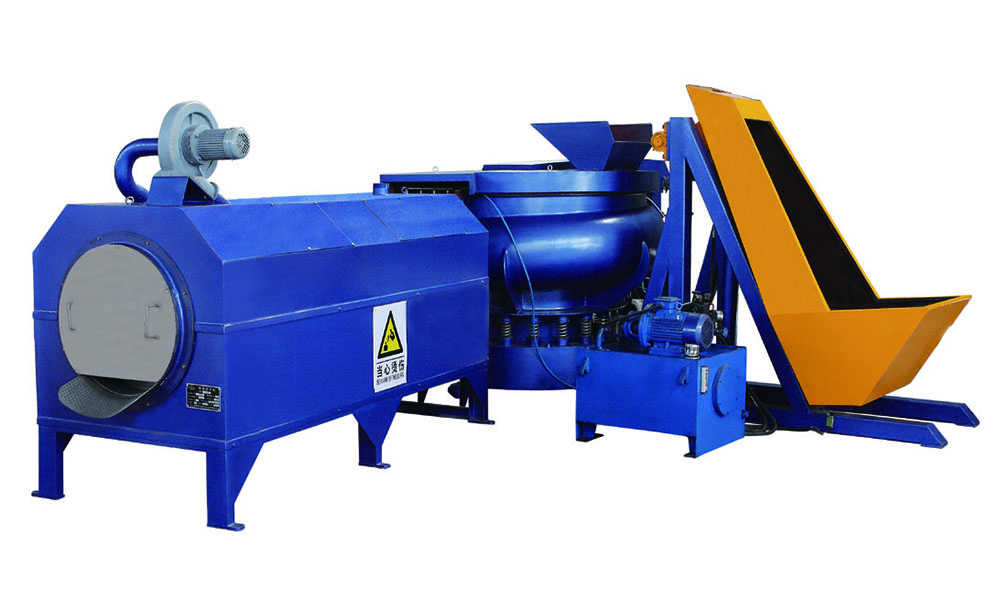
Applied to all kinds of metal parts(especially large lot small size part)deburring, cleaning, and drying.
...
Application Field
Learn More
News Center
Now the country is becoming more and more strict with environmental pollution discharge, and our products will produce a lot ...
In order to implement the national energy conservation, material saving and environmental protection policies and policies, t...
The modern electronics industry, ultra-precision polishing is the soul physical polishing is the most commonly used polishing...